Optimized Strategies to Reduce the Cost of Test and Inspection While Increasing Manufacturing Quality
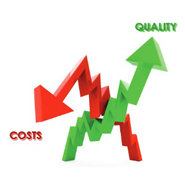
by Paul Groome, Machine Vision Products, Inc. Published in US-Tech May 2009 Edition
In the current economic environment optimizing manufacturing costs, and especially Test and Inspection costs are high on most companies agendas. But we still need to ensure the highest level of quality for customer shipments. Both cost and quality goals can be achieved by carefully selecting the test and inspection strategy used in manufacturing. Understanding the benefits and defect coverage provided by the many solutions is key to achieving the highest quality at the lowest costs.
The majority of Test and Inspection techniques used today have been around for a long time. Most originated in the late 80’s when the prevalence of manufacturing processes were using through-hole technology. Why, with the introduction of SMT manufacturing processes over 15 years ago, are we still using the same equipment and test methodologies?
Most manufacturers I have worked with use the same techniques for Test as their companies used 20 years ago, ICT, Visual Inspection, MDA and Functional Test. Is this the most efficient way to ensure process quality and the lowest costs? No. In most cases Full AOI combined with Boundary scan will locate all production and electrical defects.
If we look at today’s manufacturing processes there are a plethora of automated test and inspection techniques to find defects and add quality; In-Circuit Test Systems (ICT), Manufacturing Defect Analyzers (MDA), Full Automated Optical Inspection Solutions (AOI-Full), Comparative Automated Optical Inspection (AOI-Comp), Functional Test (FT), Boundary Scan (BScan), Automated X-Ray Inspection (AXI) and Flying Probers (FP).
Figure 1 – Typical Package DPMO Rates
Each platform has capabilities that allow for different defect spectrum to be located, all at different cost points and diagnostic resolution. So, the question is which solutions should I use to meet today’s SMT Assembly challenges?
♦Defining a Test and Inspection Strategy for today’s manufacturing processes:
The first aspect of defining a test and inspection strategy is to understand the defects you are producing and what quality levels your customers demand.
The component types, board densities, and process equipment used drive the quality of your final assembly. DPMOJ rates (Defects Per Million Opportunity per Joint) for today’s packages range from below 50 DPMOJ to greater than 15,000 DPMOJ, with Area Array packages being the most reliable to place and reflow, while fine pitch leaded devices commonly having the highest DPMOJ rates. Figures 1 and 2 detail the typical DPMOJ rates experienced with customers at MVP (Machine Vision Products). If you are a member of iNEMI or IPC there are many tools available for you to calculate the capability of your process, expected yields and defect rates. For test and inspection it is important that your system capability matches your processes capability to deliver the highest yields.
♦System Capabilities: what is the cost to capture a defect?
Shown in figure 3, each of the test and inspection tools that can be deployed in a manufacturing process have different sets of capabilities and costs associated with them. Lets discuss the in-line options available to manufacturers today.
♦In-Circuit Test (ICT) and Manufacturing Defect Analyzers (MDA)
ICT system is the fact it can provide device function coverage for digital devices. Because of the time required to generate full test models most customers today are testing digital devices using capacitive opens techniques, taking the capabilities to a lead only test. One other issue with ICT is the fact it does not test parallel components, such as de-coupling capacitors and devices with multiple power and ground connections. Therefore fault coverage on a joint basis, commonly between 65-75%, a lot less than most customers realize. When loss of electrical access because of component density and signal frequency issues is taken into account the fault coverage falls further.
Today, dependant on configuration, systems ICT systems range from below $50,000 to over $500,000. When looking at ongoing support costs, the cost of a single fixture and program for a large board (>5,000 nets) can exceed the purchase price of an AOI (Automated Optical Inspection) system. The smallest boards can still cost $20,000, and take 2-3 weeks to complete.
Combine the cost of supporting ICT/MDA systems, joint based fault coverage, loss of access, with the fact that powered up testing for digital devices is being used less and less, does ICT provide cost effective fault coverage for today’s manufacturers?
♦Automated X-Ray Inspection (AXI)
Two major types of 3D in-line AXI systems are available in the market today. These systems are based on Tomosynthesis and Laminography. AXI can provide the highest level of lead based inspection coverage, but have a number of issues associated with providing this coverage. Normally a 3D AXI platform will range between $450-750K, in most cases be unable to meet line cycle times and can provide false calls above the 5000 ppmJ range.
Programming can be complicated and slow, as the varying track densities of the PCB substrate can affect each joint causing the programmer to treat many joints as separate items (Sub-Joints).
Today unless you are specifically looking very explicit solder defects on very high cost products, it is not a viable option for most manufacturing processes because of costs and throughput.
♦Boundary Scan (BScan)
As part of the Joint Test Action Group (JTAG) boundary scan became a standard in the 1990s, showing great promise. But the adoption of boundary scan was slow until recent days where loss of electrical access has become a large issue with ICT and MDA systems. Boundary Scan, when implemented, provides the highest level of digital fault coverage at the lowest cost per defect, with solutions ranging between $10,000 and $25,000.
The key to Boundary Scan is to ensure your circuit design engineers take into account the capability. Most larger scale integrated circuits today include Boundary Scan. If your design engineers chain these devices together correctly, Boundary Scan techniques can provide very high fault coverage. Boundary Scan is one of the best tools in the industry today for digital device coverage, ISP and flash programming.
♦Automated Optical Inspection (AOI) – Full AOI and Comparative AOI
Most people bound the two different types of AOI (Comparative and Full Rules Based) systems into one category, but these two types of systems have substantially different capabilities and performance in the manufacturing process.
When new users start to look at AOI, in general they start evaluating aspects that are easy to understand like: megapixels, magnification, optics, all of this is nice to know but does it mean anything. Is a system with a 5 megapixel camera better than a system with a 4 megapixel camera? As single items, the specifications of each of the components are insignificant. The real specifications to evaluate are how the components work together which in-turn drives the pixel resolutions vs. the throughput of the systems. For 0201 style components a resolution of 16-18um will be adequate. Using a real-world example, a system may quote a 4 megapixel camera, have throughput of 5 Sq inches per second and pixel resolution of 25um while a second system could use a 5 megapixel camera provide a 7 Sq Inches per second throughput and have pixel resolution below 16um. Clearly when looking for resolution and imaging capabilities the overall system capabilities need careful critique.
♦Full AOI
Full AOI will provide you with the best defect coverage, highest throughputs, repeatability and metrology. The main reason for the increased performance is that these types of systems actually measure the parameters of a component and joint being inspected rather than comparing to a suggested good part. As such these techniques are less susceptible to process variations while providing enhanced inspection techniques to measure components and parameters of the product. Unlike Comparative AOI systems, Full AOI metrology based techniques can provide extended capabilities that can allow for full SPC, process control and component measurements.
“The techniques used by full metrology based AOI systems are far less susceptible to process variations while providing enhanced defect coverage over comparative based AOI systems.”
When choosing a Full AOI system, there are some key aspects to look at, one being the techniques used to locate defects. The most powerful of these techniques is the Tri-Color technique that allows for simple, accurate and reliable defect detection. This works by using angled light vs. angled cameras to generate solder and joint information. For example three rings of Red, Green and Blue LEDs are used at different angles (0o, 45 o and 90 o) each showing different aspects of the component, joint and solder being inspected. Figure 4 shows an example of a lifted and acceptable QFP joints that can be easily detected using these techniques.
Figure 4 – Lifted QFP cornet pin detected using Tri-Color Technology
The second point to look at is software. Many Full/Metrology based AOI systems can be time consuming to program for the first article. This is not true for all systems. Companies like Machine Vision Products have been investing heavily to remove the gap between Full AOI and Comparative AOI programming times with products such a ePro that fully automate the program generation process effectively providing you with the fastest programming times without the loss of coverage and performance you would normally see with comparative based systems.
Full/Metrology based AOI systems also lend themselves to other micro-electronics and Semiconductor environments where understanding the process and the provision of SPC data is of the utmost importance.
♦Comparative AOI
These types of systems use a golden image of a component and compare the part to the component under inspection to provide Pass/Fail information. Their focus is predominantly on placement, presence/absence, and optical character recognition. These techniques can provide a quicker initial program, but has the issue of decreasing performance in production, as variations in your process have to be taught as you see them in production. Creating high false fail rates per board. These types of systems can generate programs very quickly for first article inspection but provide significantly reduced performance and risk in production.
♦Choosing the Correct Test and Inspection Strategy
Figure 5 details the Total Defect Coverage for each type of test and inspection scenario. As discussed previously, all have different capabilities and attributes, but in today’s environment where quality and cost is key you need to choose the best solutions and most cost effective Test and Inspection equipment to meet your manufacturing needs. Full AOI clearly allows for the maximum fault coverage at the lowest cost and can be complemented by a number of different solutions.
Figure 5 – fault Coverage Capabilities, NPI and Lowest Cost Strategies
For example, if you have designed in Boundary Scan, an unsurpassed level of defect coverage can be obtained by distributing test and inspection with Full AOI. Figure 5 shows the defect coverage capability. On going costs, when distributing test and inspection across Full AOI and Boundary Scan are extremely low, minimal fixturing is required, and programming time is commonly less than a half a day. Using Full AOI also allows you to use deploy process control and using these two platforms. The deployment of Full AOI and Boundary Scan in a distributed test and inspection strategy can provide: 100% component coverage, determine the values of passives, ensure the operation and functionality of each digital component on a board while costing significantly less than any of the traditional test methods used today.
Many combinations can be used, but the obvious winner for cost reduction while still providing the ability for total defect coverage is a distributed test and inspection strategy that includes Full AOI. The Full AOI system needs to incorporate: metrology, tri-color defect detection techniques, flexible measurement capabilities, high resolution and ease-of-use programming features combined with a combination of Boundary Scan or MDA platforms.